
TF8560 is a technology package that provides all the components for controlling motion functions in plastics machines.
#DESKTOP BOARD BLOW MOLDING MCHINE SOFTWARE#
The TwinCAT 3 Plastic Framework contains three software libraries: TF8540 enables comprehensive software-based temperature control in plastics processing. As a result, plastics machines can be programmed, visualized, and controlled on a single platform. The TwinCAT 3 Plastic Framework brings together our many years of expertise in plastics, seamlessly integrating important industry-specific functions into the established TwinCAT environment. With the TwinCAT 3 Plastic Framework, we offer a modular software solution for the control of plastics machines that minimizes development effort and maintains the open nature of Beckhoff architecture. Modular software solution for the plastics industry
#DESKTOP BOARD BLOW MOLDING MCHINE FULL#
full integration of MATLAB ®/Simulink ® increases efficiency of engineering processes.Beckhoff's process know-how in injection molding technology supports the customer with software development.extremely short sampling times for high-precision switching over to holding pressure and mold securing.universal motion control architecture for electric and hydraulic axes, optimally suited for servo-electrical drive technology by also integrating drives from third parties.Euromap (OPC UA)-based communication standards for the plastics industry are integrated.cost-optimized I/O architecture for large-volume applications.EtherCAT as the Beckhoff standard for the injection molding machine industry.scalable Industrial PCs and operating devices for different machines and markets.In order to meet the high market requirements for product quality, functionality and efficiency, machine manufacturers have extensive software and hardware components from the Beckhoff product and technology portfolio at their disposal:

Maximum precision and energy efficiency for injection molding machines This reduces not only hardware costs, but also engineering effort and lifecycle costs. On the other, special devices can be omitted due to the consistent implementation of all functionalities as software modules.
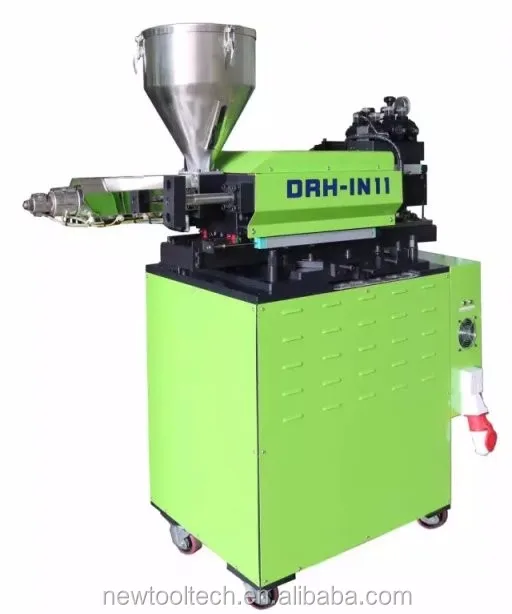
On the one hand, this ensures the efficient interaction of all system components and thus maximum productivity. The latter serves as a software platform for engineering, runtime and the diagnosis of all control functions: from PLC, motion control and robotics to HMI and vision, and from safety and measurement technology to cloud communication and analysis functions. It comprises an extensive portfolio of Industrial PCs, EtherCAT as a fast communication system, the decentralized I/O modules, drive technology components and TwinCAT automation software. The Beckhoff solution for injection molding machines is based on a universal hardware and software platform. Through support for the vendor-neutral Euromap standards based on OPC UA, EtherCAT as a fast fieldbus and TwinCAT as a universal engineering platform, the Beckhoff controller enables the realization of a wide range of heterogeneous production cells. Machine manufacturers can use Beckhoff's industry know-how or incorporate their own process knowledge – also in combination with the tested application modules, for example for temperature control. Operational reliability is additionally ensured by reverse polarity protection against phase voltage.īeckhoff's many years of experience in hydraulic and electric drive technology or temperature control led to the development of injection molding-specific engineering platforms. Up to 32 temperature channels can be contained in one industrial connector. The FM3312 and FM3332 Fieldbus Modules in a sturdy metal housing are suitable for temperature measurement on injection molds or on injection barrels. The development of EtherCAT plug-in modules for use on customer-specific backplanes for large-volume applications was driven by the desire to minimize wiring errors and achieve cost savings in switching production for small and medium-sized machines. XFC increases the accuracy of < 100 ns when switching from injection to holding pressure, thus improving part quality and reducing material consumption. The high demands of high-performance injection molding machines were a major motivation for Beckhoff to develop the extremely fast communication technology XFC (eXtreme Fast Control). From individual components to the complete solution, the user benefits from Beckhoff's broad process and application know-how in plastics processing. Beckhoff has been a development partner for the "first choice" companies in injection molding for many years.
